In industrial environments where dermal exposure to hazardous chemicals can occur, engineering, administrative, and work practice controls can minimize the worker’s contact with chemicals. Where these controls are inadequate, the use of chemical protective garments (CPG) can minimize the risk of exposure and provide the last line of defense. This guide describes to select appropriate CPG for your operations.
Chemical Protective Garments
Search this label on your garment to understand the level of protection it proposes.
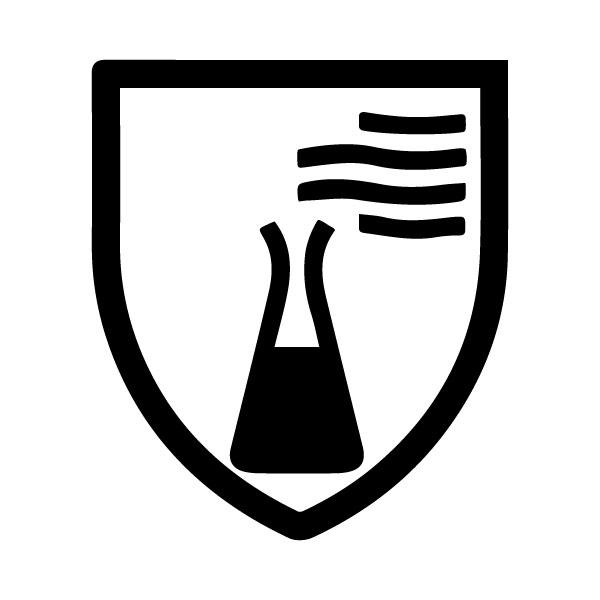
There are certain considerations with chemical protective garments. The most important one is that no clothing is "impervious," since all clothing will eventually seep in chemicals. Exposure time is the most important factor in this case. The longer aggressive substances stay on garments the higher is the risk the fabric will yield to corrosion. Discuss your administrative controls and work patterns with our sales manager to select fabrics suiting your occupational health requirements.
Steps before Contacting SGK
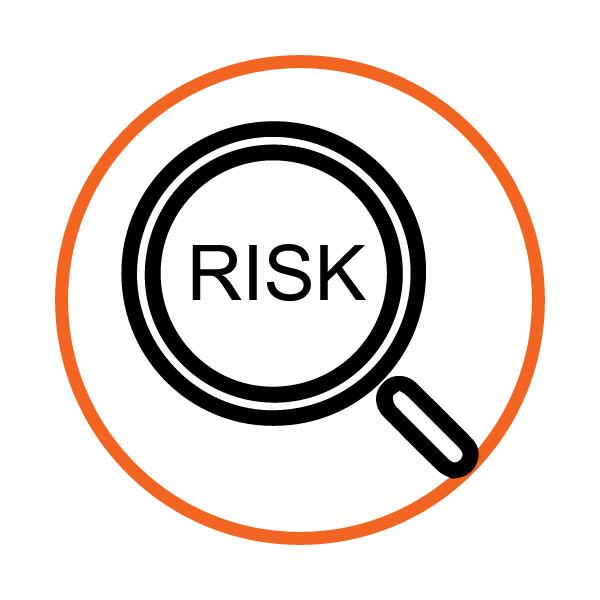
Evaluate your workplace
Before considering CPG evaluate your site to confirm all engineering controls are in place. Collect detailed information on operations conditions that matter a lot to select correct materials.
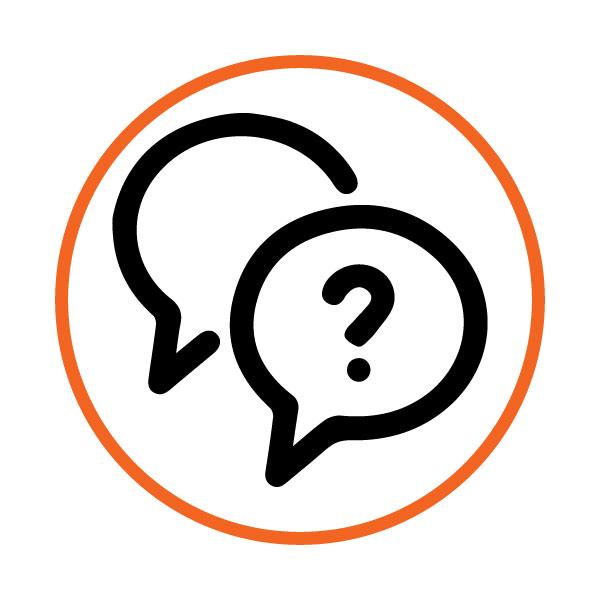
Know your substances
Fabrics are manufactured for protection against certain aggressive chemicals. We need to know what substances you work with to pick correct materials for your needs.
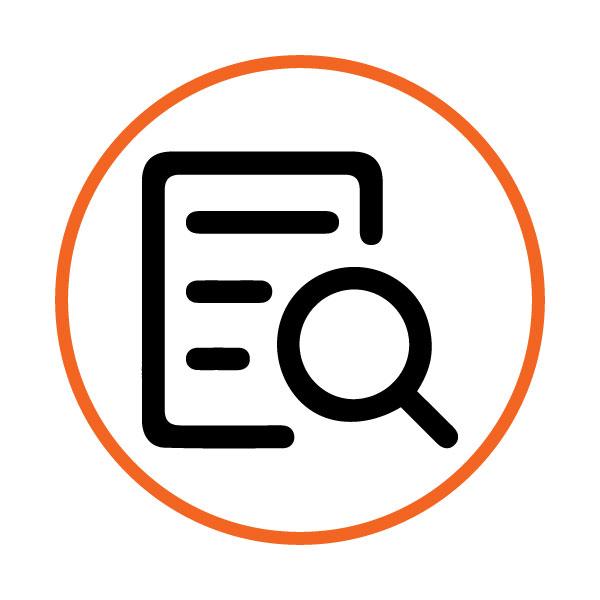
Administrative details
Exposure time matters. What are the routines in place if worker was exposed to substances? We need to know how long aggressive substances rest on garments.
It should be noted that CPG also prevents evaporation, causing skin temperature to increase and potentially increasing the permeability of skin. Thus, CPG that has not been tested for the specific operating conditions it is used in may not provide adequate protection.
The same material, even at the same thickness, may provide different levels of protection depending on the manufacturer, since different manufacturers use different processes and may add different additives. We have collected our own database of manufacturers and monitor performance of their materials based on tests upon receipt in our warehouse.
Finally, while we can test and manufacture CPG to protect from individual chemicals based on "worst-case scenario" and exposure continuity, most industrial exposures are not continuous and are in fact mixtures of chemical, for which permeation rates are different. Continuous monitoring of CPG performance and further communication of chemical erosion is important to continue increasing protective properties of materials for specifics of your operations.
Key Factors to Make Choice
When selecting Chemical Protective Garments, there are several factors that must be taken into account prior to selecting exactly what is needed. A risk assessment is often a very good tool to assist with making sure that the right protective clothing is selected. We recommend determining the following:
- The chemicals being used and their hazards.
- The state of those chemicals; for example, if they are vaporous, they could be more hazardous and, thus, a higher level of protection will be required.
- Whether anticipated contact with aggressive substance is a result of occasional splashing, or a result of more continuous contact.
- Whether the worker can be exposed from handling contaminated CPG.
- Environmental Conditions (Weather, location).
- Duration the worker will be wearing the protective clothing and how long the worker may wear contaminated garments.
- The temperature where the chemical is being handled.
- The parts of the body that the chemical could potentially contact.
- Whether the CPG resists physical wear and tear while performing the type of work being done.
- Whether the CPG interferes with the work, for instance by limiting dexterity.
Once a garment is selected, it should undergo a limited evaluation with worker training. Once the garment is regularly used it should be regularly evaluated.
Levels of protection
Levels of protection are normally based on the amount of protection for the wearer’s skin and respiratory protection.
Level A | The highest level of both respiratory and skin protection. Consists of a full encapsulating suit that is vapor tight with respiratory protection consisting of either Self Contained Breathing Apparatus (SCBA) or supplied air respirator. Used when protection from vapor and liquid is needed. Ensemble may also consist of internal radio communication, head protection, boots, and gloves. |
Level B | The highest level of respiratory protection with reduced skin protection. Consists of chemical resistant clothing that may or may not be fully encapsulating, paired with either a Self Contained Breathing Apparatus (SCBA) or supplied air respirator. Used when there is a reduced risk of vapor exposure but there are concerns with exposure to respiratory tract. Ensemble may also consist of radio communication, head protection, face shield, boots, and gloves. |
Level C | Reduced respiratory protection along with reduced skin protection. Consists of a liquid splash protection suit (coveralls) paired with an air purifying respirator. Used when there is reduced risk of skin exposure to chemicals but there are concerns with contaminants in the air. Ensemble may also consist of radio communication, head protection, face shield, boots, and gloves. |
Level D | The lowest level of protection required. Can be used where there is no chance of chemical being splashed onto the worker and there are no contaminants that would harm the respiratory tract. Ensemble consist of standard work coveralls, face shield or safety glasses, gloves, and boots. |
SGK's area of competency is to manufacture garments for Level C and D.
Protection Subdivision by Type of Substance
While level of protection above corresponds to composition of CPG and peculiarities of assembly to ensure adequate protection subdivision by material is based on the type and concentration of chemically aggressive substances and exposure time.
Note even the highest level of protection will not be sufficient for long exposure time. For instance, typical fabrics with K80 protection level that are readily available on the market in Kazakhstan and are economically attractive can resist interaction with sulphuric acid for at least six hours. When planning your operations either consider regular laundry to remove aggressive substances or consider higher level of protection.
K20 | sulphuric acid | against splashes of solutions with acid content up to 20% |
K50 | sulphuric acid | against splashes of solutions with acid content from 20% to 50% |
K80 | sulphuric acid | against splashes of solutions with acid content from 50% to 80% |
Kk | sulphuric acid | against splashes of concentrated acid with content above 80% |
Щр | against alkali melts | |
Щ20 | sodium hydroxide | against splashes of alkali solutions with concentrations up to 20% |
Щ50 | sodium hydroxide | against splashes of alkali solutions with concentrations up to 50% |
Combination of acid and alkali protection is also possible with some fabrics. Depending on your operational requirements make sure you find corresponding label of chemical protection type on your CPG.
Chemical Protection Garments